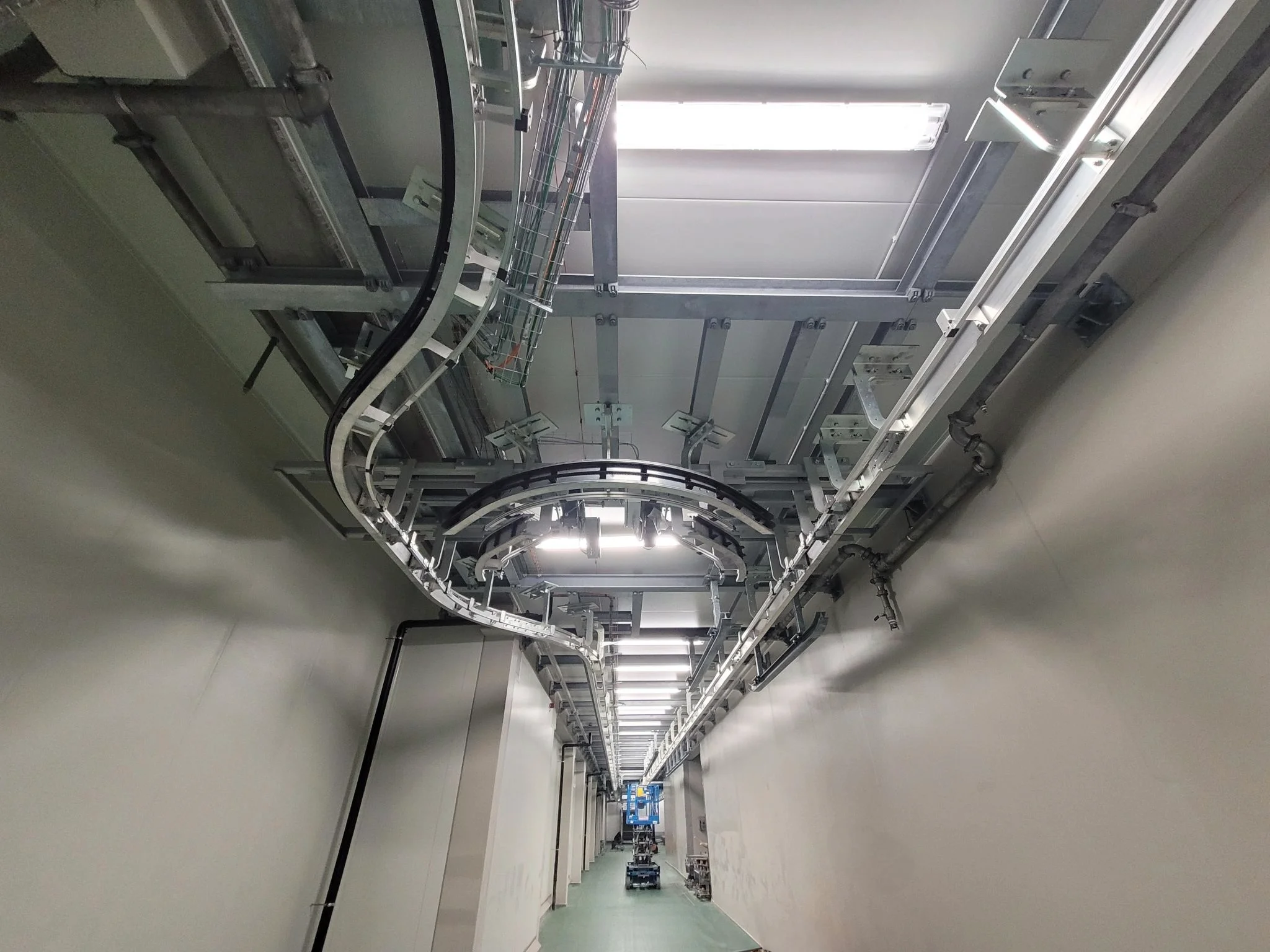
VAHLE system ensures maximum efficiency and hygienic safety in food production
vPOWER CPS 140kHZ | vCOM SMGM | vDRIVE VCS-SAFE
The VAHLE fact check
Industry
Intralogistics
Number of vehicles
11
Length of the system
270 meters
Background
One of Europe's largest meat producers, Westvlees, has built one of the most modern food factories in Staden, Flanders, Belgium. During the planning and implementation of this project, Westvlees relied on VAHLE's expertise in electrification, data transmission and control to establish a new industry standard. Westvlees produces 140,000 tons of pork products annually, making it one of the top 10 meat processors in Europe.
The challenge
Maintaining absolute hygienic cleanliness in sensitive areas of production facilities while optimizing operational efficiency has long been a critical issue in the food industry. Every step in the process - from slaughtering to packaging and labeling - requires the utmost care to ensure the highest standards of quality and safety. With the increasing demand for fresh produce in today's market, there is growing pressure to minimize processing time and maximize process efficiency.
Our solution
The conveyor system, here as an application in an overhead monorail system (EMS), was equipped at Westvlees with a complete VAHLE system, which includes vPOWER energy transmission, vCOM safe data transmission and vDRIVE control. In order to minimize abrasion and other wear as a possible source of contamination in food production, the EMS is not equipped with a conventional conductor rail system, but with the non-contact, inductive CPS 140kHz energy transmission system.
The vCOM SMGM data communication, also known as slotted waveguide, enables fast and interference-free data transmission. The transport system also benefits from the vDRIVE VCS-SAFE control system with STO function, which offers additional safety levels and enables immediate intervention in the event of system malfunctions.
The VAHLE system, consisting of inductive energy transmission, safe communication and precise control, guarantees a smooth and hygienically flawless process and sets new standards in food production thanks to its virtually maintenance-free technology.
The facts
- End customer: Westvless NV, Belgium
- Customer: UP Universelle Fördertechnik GmbH, Germany
- Year: 2023
- EMS length: 270 meters
- Number of vehicles: 11
- Solution: VAHLE system, consisting of contactless energy transmission, SMGM data communication, VCS-SAFE control system